Advantages of Positioning Labeling Machines
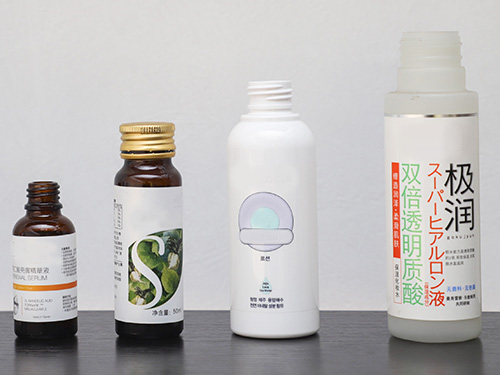
The advantages of positioning labeling machines lie in their precision, efficiency, adaptability, and intelligent capabilities, meeting the high standards of modern automated industrial production. Below is a detailed breakdown of their core strengths:
1. High-Precision Labeling
- Accurate Positioning:
Utilizes vision systems, servo control systems, or laser positioning technology to achieve positioning accuracy within ±0.1mm, ensuring labels align perfectly with design specifications and eliminating human errors. - Adaptability to Complex Surfaces:
Capable of applying labels smoothly to curved, uneven, or irregularly shaped objects (e.g., bottle caps, cylindrical packaging) without air bubbles.
2. Enhanced Production Efficiency
- High-Speed Operation:
Maximum labeling speeds reach 300–800 labels per minute, far surpassing manual operations, ideal for large-scale continuous production. - 24/7 Continuous Operation:
Automated design minimizes downtime and seamlessly integrates with production lines, ensuring stable output.
3. Adaptability to Complex Scenarios
- Dynamic Labeling Capability:
Tracks and labels moving objects (e.g., rotating bottles) on conveyor belts without stopping the production line. - Compatibility with Diverse Label Types:
Supports adhesive labels, film labels, and specialty materials (e.g., heat-resistant, waterproof labels). - Rapid Configuration Switching:
Adjusts label positions, sizes, and application modes via software to accommodate small-batch, multi-variant production.
4. Reduced Overall Costs
- Lower Labor Dependency:
One machine replaces multiple workers, cutting labor costs and minimizing human errors that lead to label waste. - Material Savings:
Precise control over label peeling and application reduces material waste (e.g., residual backing paper, misapplied labels). - Low Maintenance Costs:
Modular design enables quick replacement of wear-prone components, reducing downtime.
5. Intelligence and Traceability
- Smart Detection:
Integrated vision systems or sensors detect missing or misaligned labels in real time, automatically rejecting defective products. - Data Connectivity:
Interfaces with MES/ERP systems to record labeling data (e.g., batch numbers, timestamps), enabling full production traceability.
6. Improved Product Quality
- Consistent Results:
Eliminates human-caused issues like skewed or wrinkled labels, enhancing product aesthetics. - Durable Adhesion:
Pressure rollers, air-blowing, or roller-pressing technologies ensure labels remain intact during transportation, storage, or environmental changes.
7. Broad Industry Compatibility
- Pharmaceuticals: Meets strict GMP requirements for label accuracy and content.
- Food & Beverage: Compatible with high-speed filling lines and transparent/curved containers.
- Electronics: Applies micro-labels (e.g., QR codes, component identifiers) with precision.
- Consumer Goods: Handles diverse packaging materials (plastic, glass, metal).
8. Eco-Friendliness and Safety
- Low Noise and Energy Consumption:
Energy-saving technologies (e.g., servo motors) align with green production standards. - Safety Features:
Includes emergency stop buttons, protective covers, and safeguards to prevent operator contact with moving parts.
Summary: Positioning labeling machines address inefficiencies, inaccuracies, and high costs of traditional labeling methods through advanced automation and technology. They are pivotal in smart manufacturing for boosting product competitiveness and brand image.