Como uma máquina de enchimento de pigmentos totalmente automática alcança ±0,1% de precisão de enchimento?
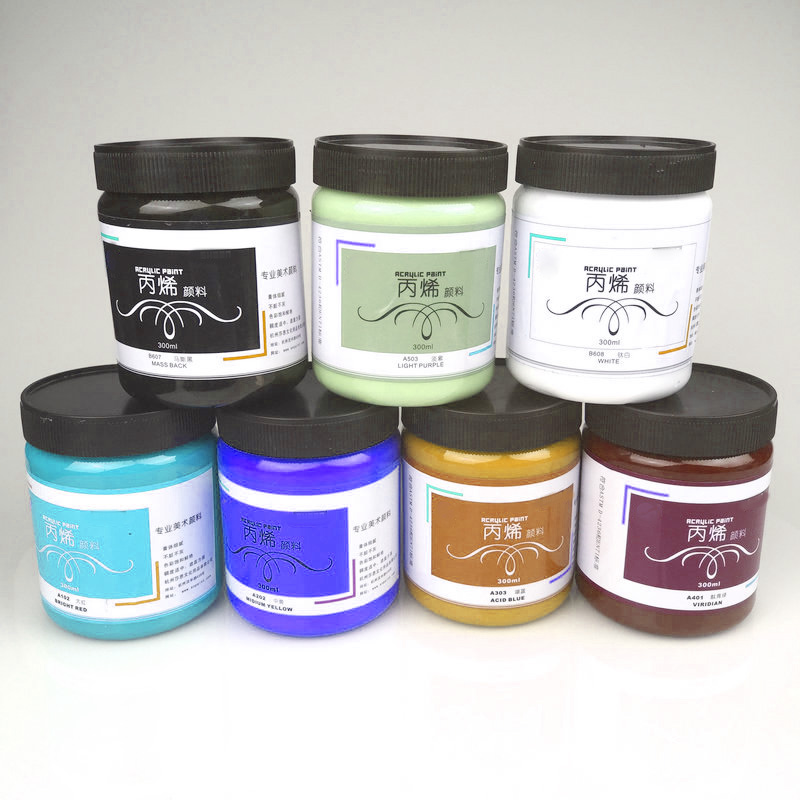
No produto químico, Revestimento e outras indústrias, A precisão do enchimento do pigmento afeta diretamente a qualidade do produto e os custos de produção. The fully automatic pigment filling machine uses three core technologies to control the filling error within ±0.1%, which completely changes the inefficiency and error problems of traditional manual filling.
1. High-precision sensing system: dual calibration guarantee
The fully automatic equipment is equipped with a weighing sensor + electromagnetic flowmeter dual detection module:
The weighing sensor monitors the weight of the container in real time with an accuracy of 0.01g;
The electromagnetic flowmeter dynamically tracks the pigment flow rate and automatically corrects the pipeline pressure fluctuation;
The dual system data cross-verifies, and the error exceeds the limit and the alarm stops immediately.
2. Intelligent servo control system: millisecond-level dynamic response
The switching delay of traditional pneumatic valves can easily lead to overfilling, while the fully automatic equipment adopts:
Servo motor driven pump: flow control accuracy of 0.1ml/pulse;
Closed-loop feedback system: automatically adjust the filling speed according to viscosity changes;
Anti-drip design: 0.3ml residual liquid is sucked back instantly after filling to avoid wall hanging.
3. Environmental adaptive compensation technology
For variables such as temperature and viscosity, the device has built-in:
Temperature sensor: automatically adjusts the insulation pipe to prevent pigment condensation/volatization;
Viscosity adaptive algorithm: dynamically optimizes the pump speed through the pressure-flow model;
Data traceability system: records the filling parameters of each batch and supports quality traceability.
Application scenario: Filling metallic paint in a low temperature environment of -10℃ can still maintain ±0.2% accuracy.